Pickering pedestrian bridge nears completion after years of delays
Following years of delays and issues with the contractor, the pedestrian bridge at the GO Station in Pickering, Ont. is on track to be complete by the end of the summer.
The 250-metre bridge is one of the longest enclosed pedestrian bridges in the world and crosses 14 lanes of traffic on Highway 401 and six tracks along a rail corridor. While construction on the bridge started in 2010 and was substantially complete, opening to the public in 2012, six years later, there is still work to do to fully complete the project.
“A beam associated with the support structure for the cladding was installed incorrectly and as a result, the bridge cladding could not be mounted to the structure as it would not fit as designed,” stated Nick Spensieri, director of corridor infrastructure for Metrolinx, in an email to the Daily Commercial News. “This misalignment and the contractor’s refusal to fix the misalignment was one of the primary reasons for termination on the second contract. This, as well as the ‘careless welding,’ is why the contractor was fired for ‘poor performance.’”
The Pickering project’s challenges were also cited in the 2016 Annual Report of the Office of the Auditor General of Ontario.
“The contractor for Phase 1 of the construction of a pedestrian bridge over Highway 401 in Pickering performed so poorly that Metrolinx staff had to take over performing many of its duties, nevertheless, Metrolinx hired the same contractor for Phase 2 of the project because it was the lowest bidder,” indicates the report.
“On Phase 2, the contractor caused significant damage to the bridge…Metrolinx terminated the contract with the contractor because of performance issues, even though the construction had not been completed, and paid the contractor almost the full $8 million of its contract.”
Another contractor needed to be retained to finish the work, which is now expected to be completed by the end of August.
Phase 1 of the project involved the construction of the bridge structure and stairwells and Phase 2 involved the installation of a Kalzip cladding system, a lightweight aluminum-mesh product used as the “skin” for the new bridge, which is where the contractor ran into problems, explained Spensieri.
“They got across the main span of the bridge and then ran into some difficulties on the stairs as they went down on either side so the project came to a halt for a good year and a half,” he said.
Also, some of the glass panels on the bridge cracked because they were not properly protected prior to welding work being done by the previous contractor, states a recently issued Q&A with Roberto Sguassero, a project manager for the Pickering bridge installation.
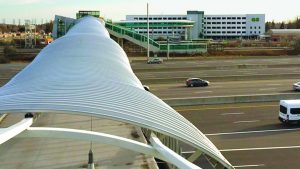
“The splatter from the welding damaged the composition of the glass, which maintained its shape and structural integrity despite being broken,” the Q&A explains. “We continue to work with our supplier who is obtaining the glass from Montreal for the replacement sheets, which take a while to temper and laminate since each sheet is so large and heavy.”
The second phase of the project also includes an LED lighting system similar to the one at the CN Tower which lights up in different colours.
Electricians are placing the remainder of the LED fixtures which will illuminate from under the cladding, Spensieri said.
The bridge is made up of seven box trusses, weighing several thousand pounds each, which were transported using one of the largest mobile cranes in Canada.
According to a release issued by Metrolinx, the trusses were installed on the concrete piers which were constructed off the rail corridor and in between the 401’s collector and express lanes. Once the trusses were in place, the concrete pad was poured on the bridge’s floor and the windows and roof were installed.
Although there was mention in the auditor general’s report that a truss had been installed upside down, Sguassero said it would be impossible because they are designed to go one way and are so massive that they are difficult to manoeuvre. It was a support beam, not a truss, that was installed out of alignment, Spensieri explained.
“They have to be transported and lifted by a crane at very specific points on the truss — this is verified by engineering drawings and triple checked by a dozen engineers onsite to oversee the lift,” explained Sguassero in the Q&A.
“They’re designed with an arch that flattens out when the feet of the truss land on the concrete piers. Theoretically, the arch would get bigger if you tried to install the truss the wrong way, making it virtually impossible to get into place.”
By Angela Gismondi
Daily Commercial News
Redes Sociais - Comentários